Choosing the right speed sensor for an application is of crucial importance for an accurate and reliable measurement. After all, the signal of the sensor is the input for an overspeed protection system. A faulty sensor leads to an unreliable input signal and has a negative influence on the accuracy and reliability of the protection system.
There are several considerations that have to be made when choosing the right sensor, which can be categorized in environmental and machine considerations.
Machine considerations:
- What is the expected RPM-reach?
- What is the target that is measured and what are its specifications?
- Are there any limitations on the weight and size at the mounting location?
- What is the necessary cable length?
Environmental considerations:
- What is the expected ambient temperature?
- Does the measurement take place in explosion hazardous areas (ATEX)?
- Are strong electromagnetic fields present?
- Does the measurement take place in a corrosive environment
For industrial speed measurements there are three main types of measurement principles:
- Electromagnetic sensors – also known as: passive sensors, variable reluctance (VR) sensors or magnetic pickups
- Proximity sensors – also known as: eddy current sensors or displacement sensors
- Hall-effect sensors – also known as: active sensors
Electromagnetic sensors
An electromagnetic sensor uses a magnetic field to measure changes in the distance between the sensor tip and the target object. The sensor contains a coil that is wrapped around a magnet which cause a change in the magnetic current (flux) and the coil as the teeth of a gear pass the sensor. The moving gear creates a varying flux that induces a proportional voltage in the coil of which the frequency is related to the rotation speed. The signal is a sinusoidal wave of which the amplitude depends on the target size, speed and distance.
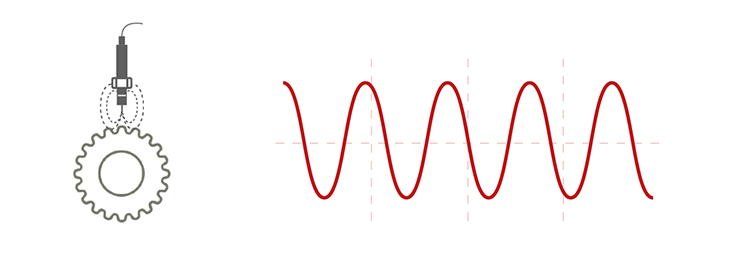
Advantages
An advantage of electromagnetic sensors is the applicability to high-temperature applications. There are specific types of sensors that are suitable to function with temperatures of more than 300°C. Moreover, electromagnetic sensors are easy-to-use and highly reliable . Another big advantage is that the sensor has a two-wire connection and therefore often fits within existing infrastructures.
Disadvantages
A major disadvantage of electromagnetic sensors is that the amplitude of the signal depends on a factor of the size, speed and distance of the target. If the speed is too low, the gear tooth too small or the distance to the target material too big, the signal will be too flat. On the other hand, if the speed is high, the gear tooth large or the distance is small, the signal will show huge pulses (up to 80V). The application and positioning of electromagnetic sensors requires a lot of attention and expertise for the proper functioning of the sensors. As these type of sensors do not function well with low speeds, they are not suitable for zero-speed detection.
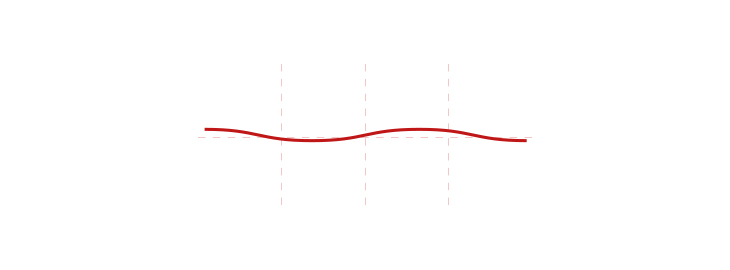
Proximity sensors
A proximity sensor uses an electromagnetic field to measure changes in the distance to an object. As a gear moves past the sensor, it measures a variation in distance; close (tooth) and far (notch). The rotation speed can be determined based on the time between these events.
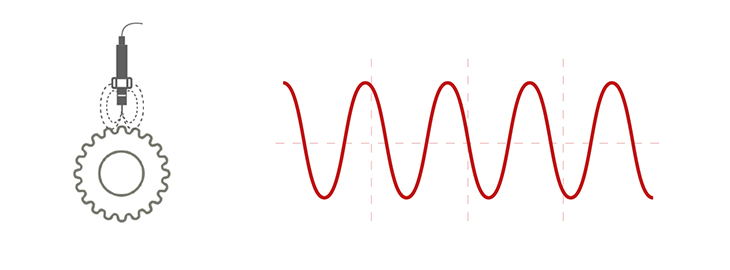
Advantages
A major advantage of proximity probes is that the measuring principle shows both the pulses and the position with respect to the teeth. This provides insight into the set distance to the teeth of the target.
Proximity sensors are also available with a dynamic current output, which allows for very long cable lengths (1000m+). Sensors with a dynamic current output are not influenced by cable impedance, as is the case with proximity sensors based on voltage signals, Hall effect and electromagnetic sensors.
Disadvantages
The use of proximity sensors for speed measurements has a disadvantage. At a high speed (RPM), saturation may occur, as a result of which the sinusoidal line is increasingly flattened. When the gear tooth move past the sensor at high speeds, a proximity sensor barely detects a difference in distances. The higher the speed, the less effective a proximity sensor will be for speed measurements.
Another disadvantage is that a proximity sensor cannot handle eccentricity of the target well. Eccentricity of the target (a swinging gear) generates a sine within a sine. This leads to issues, especially when signal saturation occurs to the relevant signal. The sensor may output the sine of the gears’ eccentricity instead of the sine of the tooth and notches.
Hall-effect sensors
A Hall-effect sensor measures changes in the magnetic flux between the magnet and the target material. The sensors have built-in signal conditioners, which generate a clear square wave signal. In contrast to electromagnetic sensors, Hall-effect sensors are sensitive to the size of the magnetic flux rather than the speed of which it changes. Hall effect speed sensors have a broad measurement range and can be used to measure both low-speed or stationary parts and high-speed parts.
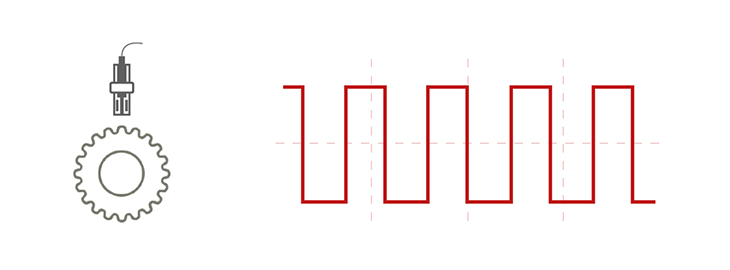
Advantages
An advantage of a Hall-effect sensor is that the sensor directly provides a digital output which is easy to transmit and process. Another advantage is that Hall-effect sensors usually feature internal signal processing. The signal is digitalized and amplified very fast, making it less vulnerable to interferences such as EMI (electromagnetic interference).
Disadvantages
Due to built-in electronics, Hall-effect sensors are limited to applications that operate in temperatures ranging from -40 °C to + 150 °C. Moreover, Hall-effect sensors require a 3-wire connection.
Why Hall-effect sensors are preferred:
- Reliable speed registration from standstill. The makes it possible to measure from frequencies as low as 0,1 Hz.
- Digital signals are suitable for long distances (up to 300m).
- Square wave signals are easy to process by speed systems.
- Possible to build two sensor elements in one sensor housing, enabling direction measurements.
- The construction of the sensor is smaller and lighter (weight) than other speed sensors.
- A Hall-effect sensor is less difficult to position correctly than an electronic sensor and less sensitive to eccentricity of the target than proximity sensors.
- This sensor type is the least sensitive to vibrations and temperature fluctuations.
See also: Overspeed protection systems »