The AirSafe from Envea (formerly SWR) is a measurement instrument designed to monitor dust concentration in ambient air. Envea’s tribo-electric sensor technology has proven its reliability in thousands of applications where dust concentrations in process systems are measured. Examples include monitoring in the vicinity of control systems, silos, boiler houses, or workstations.
The AirSafe monitors dust concentrations based on pre-set thresholds. One application is preventing dust accumulation in explosion-prone areas. The AirSafe can be used for the early detection of dust, which can pose a danger in the workplace.
Operation
The AirSafe consists of an airflow channel and a tribo-electric dust sensor. Dust particles carried by the airflow pass by the sensor, generating a charge transfer that is used as a measurement signal. This signal is then converted into an electrical output that can be used for display or control purposes.
Description
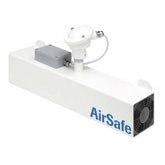
The integrated dust sensor has a relay output that activates when the pre-set threshold is exceeded. The AirSafe comes pre-calibrated with an alarm threshold of 25 mg/m³ of dust. The user can adjust this alarm threshold within a range of 5 mg/m³ to 150 mg/m³, in increments of 5 mg/m³.
The sensor features a relay output as well as an RS 485 output, which can be connected to a DIN-rail transmitter. The transmitter provides a standard 4-20 mA signal but also includes a ModBus RTU RS 485 output for PC connection. Visualization software allows for up to 10 measurement points to be visualized and stored.
Installation and Setup
The AirSafe can be installed anywhere within a room, keeping in mind the operational temperature range of -20°C to +60°C. The AirSafe can be mounted on the wall using the provided brackets. The sensor can be located up to 300 meters away from the transmitter.
The AirSafe offers several key benefits:
- Prevents the creation of explosive dust zones
- Monitors dust concentrations in workspaces
- Quickly detects dust escaping from system components
Case Study
Istec was called in by Quaker Oats Rotterdam due to an issue that arose during the delivery of wheat/oats to their factory in Rotterdam. This case describes how a room became filled with wheat due to a weak spot in
the system, and how the cause
was addressed using a specialized sensor.