Rotating machinery such as turbines, pumps and compressors are continuously subjected to major mechanical forces. As most of these machines are critical to the process, systems are implemented with protection and/or monitoring functions to prevent failures. In this article we highlight a few common speed-related failures that may occur with rotating machinery.
Speed protection
1. Overspeed
The construction of rotating machinery is designed to withstand a certain rotation speed, known as the construction speed. When overspeed occurs the shaft of the machine rotates faster than the machine construction is able to withstand. The forces increase exponential with the rotation speed which can cause parts to come loose. This could have a catastrophic impact on both the process, personnel and the environment. Risk analyses therefore show that in most cases it is mandatory to have an overspeed protection system. Through speed measurements the rotation speed (RPM) can be measured. An overspeed protection system ensures the rotation speed to stay within certain limits, to prevent damages to the machine. If the predefined limit values are exceeded, the machine is switched off immediately (Figure 1). These machine trips need to happen within a very short timeframe. According to the current machine guidelines (API 670), overspeed protection systems must have a response time of no longer than 40ms.
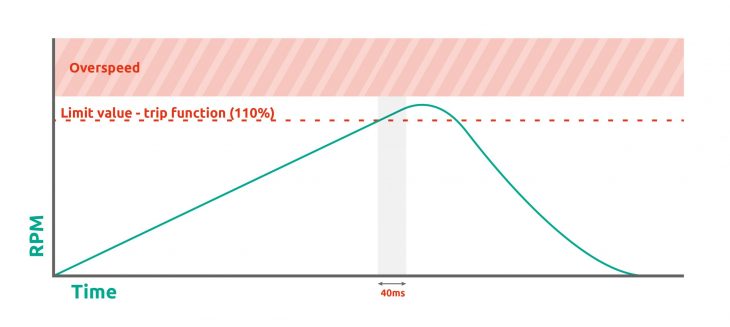
Overspeed is the biggest fear of any operator of rotating machinery. Not responding in time or the malfunctioning of an overspeed protection system could cause turbine blades or rotor parts to come loose. In the worst case, these parts go right through the turbine housing, compromising personnel safety and causing major damage to the equipment powered by the turbine.
2. Acceleration
Too rapid acceleration of a rotating machine can cause a rotating machine to go into overspeed despite the present overspeed protection system, causing a dangerous situation. Depending on acceleration speed, stopping the driver of a machine will not immediately lead to a decrease in the rotation speed. Due to major forces the speed may even increase from a short time after the driver has already been stopped. When an overspeed protection system trips when the limit value of 110% of the maximum tolerable rotation speed is reached, a certain degree of acceleration can still cause the accrued speed to exceed the allowable 110% (Figure 2). This way the machine still reaches a critical rotation speed, with damage as a result.
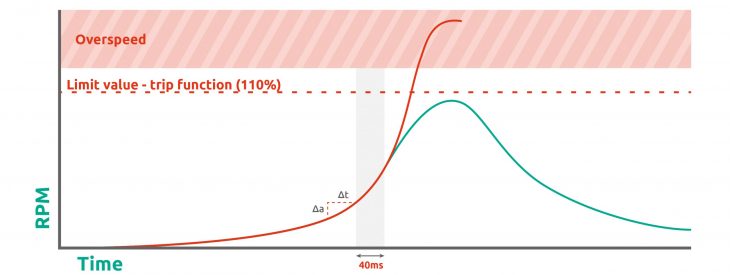
During the start-up of a rotating machine, depending on the available energy, it should be protected for acceleration. Unlike with overspeed protection, acceleration protection does not only look at the RPM, but at the increase of the RPM within a predetermined time interval. When the speed sensors detect an excessive acceleration increase, the protection system will trip the turbine.
When the machine is not protected for acceleration, it will still go into overspeed. An overspeed protection system is not capable of stopping the machine in time during an excessive acceleration increase.
Speed monitoring
3. Reverse rotation
It may occur that pressure from the process causes a compressor to turn in the wrong direction while the turbine that drives this compressor is not operating. This is known as reverse rotation. This pressure can occur because the suction valve does not close properly, causing a leak. When the turbine is started up during this condition of the compressor, this will lead to damage. The pressure that is built up as a result of reverse rotation and the pressure from the turbine will counteract each other, which may for example cause damage to the coupling. This often concerns financial damage, but does not pose a direct danger to personnel and the environment.
4. Standstill / Creep
It is important that a turbine actually stands still before turnaround / maintenance work is started. After all, the enormous mass of a turbine can cause dangerous situations if maintenance work is started while the turbine is still rotating slowly. To monitor this, speed measurements must be made over a longer period than normal speed measurements because the turbine is running at a very low speed during its shutdown process.
5. Underspeed
Underspeed is the opposite of overspeed, but is a less critical failure. To keep a process running, an installation must maintain a minimum RPM. The process can no longer be driven with a lower RPM. Although underspeed is highly undesirable due to a disruption of the production process, it does not have the same catastrophic impact as overspeed. Limit values can be set so that an alarm is triggered when the minimum RPM to keep the process running is reached. This allows the operator to prevent underspeed from occurring. Underspeed measurements can also be used to indicate, for example, that a jog engine can be switched on.
Istec hardware
The SpeedSys 200 is a SIL2 certified overspeed protection system. The robust design with advanced self-monitoring, galvanic separated in- and outputs and certification by design make a high-end product that stands out in the market. The focus on the core safety functions make a system that is easy to use and to maintain, with very long proof test intervals.
Read more about the SpeedSys 200 »
To test and verify overspeed protection systems, Istec has developed the IST-101 Frequency Generator. This tool simulates speed signals, which allows the trip function of a protection system to be fully tested without creating an actual overspeed situation.